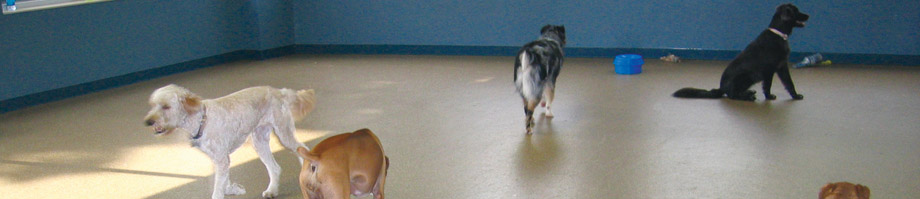
Four Factors for Flooring Success
Part 4: Flooring maintenance
More than Cleaning and Disinfecting
By Grant Loyd
Floor maintenance is more than cleaning and disinfecting your floors to avoid odors. In animal care facilities, floor maintenance issues are hard to separate from broader issues of infection control, sanitation, and odor control. Floor maintenance really includes several activities:
- Preventive maintenance actions designed to extend the life of your flooring, such as using entrance door mats, proper methods of moving furniture and large items, and dust and grit control
- Cleaning/disinfecting actions
- Actual floor product maintenance
While there are maintenance-free flooring options (such as European Safety Flooring), the majority of flooring treatments in animal care facilities need to be periodically refurbished to extend their life span.
The first three articles in this series were 1) Suitability and Quality of Products, 2) Floor Preparation, and 3) Flooring Installation. In this final article of the series, we’ll look at the above breakdown of flooring maintenance issues from an applied or practical point of view. Rather than get into details of various chemicals and choices for cleaning and disinfection, we will focus on practical things you can do to extend the performance and life of your flooring.
Preventive Floor Maintenance
In the hustle and bustle of operating an animal care facility, it is difficult to remember that floor maintenance is more than cleaning and disinfecting. That is why this article started out by listing three areas of floor maintenance. While cleaning and disinfecting are critical and must be done on a daily basis, it is not sufficient to protect your investment in your floor and to reduce the potential for loss of income associated with inadequate floor maintenance.
To start, let’s assume that you have just finished installing new flooring. The maintenance you do will play a big part in how long your flooring lasts and how it performs. Long down times are very costly, from immediate cash loss to the possibility of long-term customer loss due to being closed. Doing all three types of maintenance can significantly reduce the necessity for and length of extended “shut-down” periods because floors have to be redone.
Preventive maintenance consists of common sense things that can be done to avoid unnecessary damage to your floor and reduce maintenance costs and time. Preventive maintenance actually begins when you decide what kind of flooring you will get.
One common example is the difference between gloss (shiny) or matte (not shiny) floors. While many people like the appearance of a glossy, shiny floor, it does require more maintenance than matte or duller finishes. Very shiny floors show micro-scratches more readily than flatter, sheen surfaces. Higher traffic areas, such as entry ways, aisles, etc., will show a loss of sheen or gloss more readily than surrounding areas. To keep the floor looking as nice as possible, these worn areas need to be redone to maintain an even sheen.
However, you can avoid frequent maintenance of glossy or shiny floors by installing floors with lower sheen, such as satin or matte floors. I always recommend matte floors for lower maintenance.
A second consideration in selecting flooring, which has a great deal to do with how much maintenance is required, is color variation. A floor that is multi-colored or varied in color or intensity of color will require less maintenance than an evenly applied single-color floor. A single, evenly colored floor shows traffic patterns more readily than “color varied” floors. To keep a nice appearance, evenly colored floors require more maintenance.
By starting preventive maintenance when you make your initial flooring selection, you can save a lot of money and time over the long run and have nicer looking floors.
Now that you have your floor down, what can you do to reduce maintenance?
This is the first “maintenance” thing you can do after the floor is installed: stay off of it until it has had time to cure, and treat it carefully when moving heavy items. Very often, facility owners have scheduling issues when floors are installed. Whether a new facility or a renovation, it seems there can never be adequate time allowed to get the job done in the best way. If you do not schedule sufficient time for a floor to cure and get on it too early, you will get to see firsthand the importance of understanding “floor maintenance” as an issue bigger than odor control and hygiene.
For most types of flooring, one of the main “damagers” is grit/sand tracked onto the flooring surface and then ground in by traffic. Check exterior areas for the presence of dirt, grit, and sand. Make sure to clean regularly these exterior areas with brooms or weed blowers to reduce tracking into your facility. Install exterior mats or carpet mats to collect debris before it gets carried into the building. Next, install rubber-backed carpet mats (or similar) just inside the entrance doors.
Finally, “dry clean” by sweeping, mopping, or vacuuming these areas frequently to control the grit and sand coming in from outdoors. If you only clean these high-traffic entrance areas when you do a daily “wet” cleaning and disinfecting, you will not be effectively preserving your flooring. These areas may require more frequent attention to prevent the grit and sand from being ground in due to traffic.
As expected, most people in animal care facilities are focused on odor and sanitation. As a result, it is easy to miss or ignore floor maintenance activities that are not necessarily related to odor or hygiene. Try to develop a personal awareness and pass on to employees that floor maintenance is very much more than controlling odor and maintaining sanitation. Preventive and product maintenance activities are really money and time savers that extend the useful life of your floor and reduce the need for down time.
Probably the next worst “damager” to flooring is how people treat the floor when moving heavy items. Virtually every floor can be abused and damaged. Obviously, some surfaces are more prone to damage than others, but precautions should be taken and included in staff training for all floors.
The precautions are focused on preventing scraping, gouging, and scratching that occur when chairs, desks, filing cabinets, dog crates, pallets, or any other heavy items are pulled across a floor. Lift or use furniture movers. Do not scrape the floor. Lack of attention or laziness will cost you dearly to correct the problem. Keep in mind that required closing to repair floors can cost you more than lost income. An ounce of prevention is truly worth a pound of cure when it comes to floors.
Cleaning and Disinfecting
Cleaning and disinfecting are critical needs in every facility. What cleaners and disinfectants you use is not in the scope of this article. However, there are a few practical points that are worth mentioning due to how often the points are apparently ignored.
Bleach is NOT a cleaner. It is only a disinfectant. Biological debris, dirt, etc. will render bleach ineffective. Therefore, floors should be cleaned first and then disinfected with bleach if that is your choice. There are some disinfectants that are also cleaners, but bleach is not one of them.
Bleach needs to be rinsed very well. When diluted, bleach dries onto the floor (i.e. when all the water you added to the bleach evaporates, you now have something approaching 100% bleach on the floor). It is caustic. It is not friendly to dogs’ pads nor to floor finishes. As if that were not bad enough, it also makes floors very slippery. In one case that comes to mind, the heavy use of bleach without sufficient rinsing literally resulted in making a highly slip-resistant floor (.8) virtually unusable. In other words, the residual bleach overrode the slip-resistant nature of the flooring.
If you use bleach, rinse and rinse. You must remove the bleach from the floor, or you will pay the piper. If you have this situation now, repeated cold-water rinsing is a good remedy. The importance of rinsing cannot be overstated.
It is not just with bleach that you need to rinse well. Most cleaners and disinfectants contain surfactants and agents that end up leaving a scum on the floor if not rinsed well. Over time, you can see floors get dirty looking or dingy due to the build up of this scum and how it collects dirt. Secondly, surfactant scum will override built-in slip resistance, and you will have slippery floors. A remedy for surfactant scum is to use a 10% solution of clear ammonia and water to clean the floor. It will cut the surfactant, and then you can rinse well and have a clean floor.
When using ammonia, make sure the area where you’re working is well ventilated. In addition, do not use ammonia around open flames or in the presence of chlorine bleach. Mixing even a small amount of ammonia and chlorine bleach will cause a chemical reaction and will release chlorine gas, which can be extremely hazardous to your health.
Discussions of floor cleaning invariably come down to the issue of what tools to use. Mops are everywhere, but unless you are fanatic about keeping the rinse water and mop water clean, you are essentially moving around and leaving dirty water on the floor.
My advice is to avoid mops completely. Instead use brushes, brooms, foam squeegees, and vacuums if drains are not available. Autoscrubbers work well. Central wet vacuum systems are also very efficient and handy. But mops? Not if you want a clean floor. For disinfecting, mops should be avoided in favor of sprayers.
Actual Floor Product Maintenance
The third type of floor maintenance is actually reapplying the top product on the floor. This may be the clear coat over the system or a sealer on rolled rubber. Epoxy floors and many other fluid-applied floors are finished with a clear coat. The purpose of the clear coat is to protect what is under it (e.g. the epoxy). You need to reapply these protective coatings or sealers periodically in order to extend the life of your flooring.
Folks typically want to have the longest lasting floor or most durable floor they can. Unfortunately, what happens most often is they do not do this type of maintenance on a frequent enough schedule. Hence, they end up having to do major overhauls involving grinding or removing the failed flooring and starting over from square one.
Do not make a habit of trying to see how long you can go without doing anything to your floors. Instead, get set in your mind that periodic preventive maintenance is what extends the life of your floor and saves you money.
In conclusion, make sure that you understand the value of all three kinds of floor maintenance, and then train your staff in these same principles. Paying attention to and implementing preventive maintenance and actual floor product maintenance along with cleaning and disinfecting will pay huge returns.
Grant Loyd is the owner of DogKennelFloors.com and SolvingConcreteProblems.com. He has specialized in animal care facility flooring for 11 years and in concrete protection, including decorative concrete options and coatings, for 20 years.