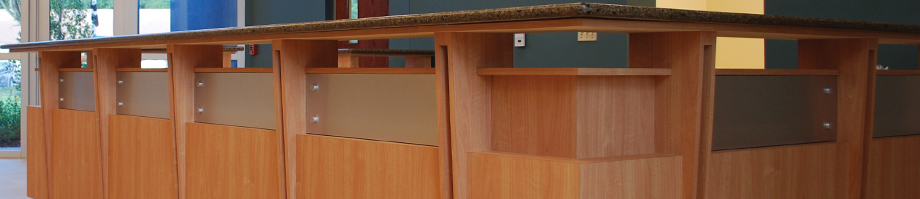
A Place to Put Your Stuff
Cabinetry construction, materials, and finishes
should match the cabinet’s location and intended use.
By Rick Bacon, AIA
One of the late George Carlin’s most famous comedy routines is about having a place to put your stuff. Animal care facilities have a lot of stuff, and the place in which you put your stuff is what the design community refers to as cabinetry. Millwork and cabinetry are cousins, with millwork usually referring to wood components ready made by a lumber mill, such as doors, window casings, baseboards, and crown molding. Cabinetry, for our purposes here, includes base and wall cabinets, drawers, and compartments for safekeeping or displaying objects, a.k.a. your stuff.
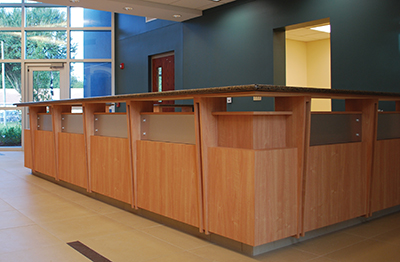
Reception desk with wood-grain laminate finish, metal-look plastic panels, solid surface counter top and tile toe-kick presents a professional image to customers. (All photos by Bacon Group, Inc.)
In an animal care facility, I divide cabinetry into three locations: 1) reception and lobby areas, 2) animal housing and work areas, and 3) staff areas. The cabinetry design for the public reception areas, including the reception desk, should include nicer materials and greater aesthetic appeal. Cabinetry in the animal housing and work areas is subject to greater wear and tear and should be functional and durable. The cabinetry in staff areas, such as the break room, is the most conventional. I recommend different construction materials, finishes, and hardware to match the location and function of the cabinetry.
Cabinetry Construction
The structural materials used to manufacture or construct cabinets range from particle board, different grades of plywood, solid wood, and metals like stainless steel. I shy away from particle board, because it is not overly durable and can absorb water more easily if exposed. Of greatest concern to me are the cabinets in the animal housing and work areas, such as food preparation and storage, grooming, and work surfaces in animal housing. These are heavy function areas subject to the most abuse and moisture.
Consider constructing cabinets in the animal housing and work spaces using marine grade plywood and plastic laminate veneer. Marine grade plywood uses the best grades of glue between the wood laminations. Although the Architectural Woodwork Institute does not recommend applying laminates over marine grade plywood, I have never had a problem with delamination. Exterior grade plywood would be the next best choice; the glues aren’t quite as good, but this grade plywood still offers high performance.
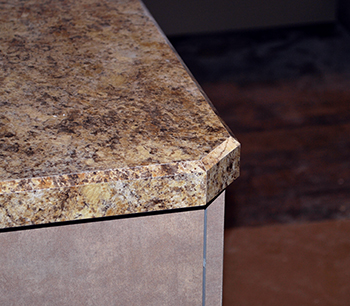
Beveled edge counter tops are a nice finish detail and less likely to chip.
In staff areas, including the break room, restrooms, wet bar, etc., standard cabinetry should be alright. Buying cabinets from Ikea or Home Depot, for example, is always an option. I have had clients tell me that less expensive cabinets would be just fine in these areas, knowing that in three to five years, they may need to replace them. You can still have nice colors that can be coordinated with the other room and building finishes palette.
Lower cabinets normally include a wood support base on the floor, which is protected by materials such as a vinyl or rubber vertical base. Inevitably, the water from mopping or hosing the floor seeps under the base and eventually deteriorates the wood, and the base cabinet will start to fail. Consider constructing a concrete base and applying the floor finish material on the base. We often wrap the resinous flooring up the base to continue the flooring system. Tile base with epoxy grout has also been successful.
In some locations in the animal housing areas, such as laundry or examination rooms, consider cabinets with sliding doors. Sliders do not need floor or upper space to open like swing doors. Doors with glass lites on the upper cabinets will allow staff to see if supplies need replenishing. If rapid access is needed or restocking is frequent, consider simple open, adjustable shelving for some or all the upper wall-mounted cabinets.
Laminates and Finishes
Visual first impressions are important, so make the cabinetry in your public and reception areas reflective of your business model. Consider using wood front veneers or panels instead of laminates. Wood may be used in bull-nose edging in some locations. A “club” look might have a cherry or mahogany finish, a “spa” look may be in bamboo, and a “modern” look might use a metallic finish. A matching wainscot in even a limited area is a nice way to extend your design motif. Textures and special finishes, like gloss and metals, will be more expensive. The aesthetic is limited only by your imagination (and maybe your bank account).
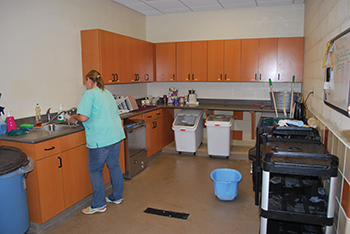
The base cabinets in this food prep room have a solid surface counter top and are elevated off the floor on concrete pads.
Laminates intended for vertical and horizontal surfaces are different. Horizontal surface laminates provide greater wear resistance than laminates for vertical surfaces. Use a standard white melamine laminate for the cabinet’s interior surface. Just remember that higher quality laminates are more chemical resistant, which, for cabinetry in animal housing work areas, is a desirable characteristic.
Counter Tops and Work Surfaces
In animal housing and work areas, I recommend a solid surface finish such as Corian or similar product, because it can handle scratches. When a mar or scratch does occur, the solid surface can be sanded and buffed, and the blemish will be removed. Standard laminate tops are less expensive but can chip, exposing the substrate, or buckle from age or water intrusion. Beveled or rounded edges and corners on counter tops are good, because they are more durable and chip resistant. I have even used refurbished white marble countertops for smaller freestanding work islands.
Task lighting, often mounted under the upper cabinets, is desirable. With all the new low voltage lighting now available, bright lighting at cool temperatures improves the work areas. Also, don’t skimp on electrical outlets accessible to your work task areas. For safety reasons, your outlets should be grounded like GFCI (Ground Fault Circuit Interrupt) receptacles with a test and reset button.
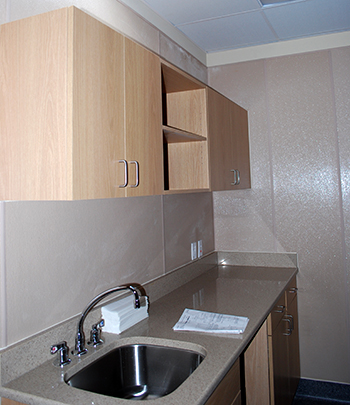
The work area in this cattery has solid surface counter tops and upper wall cabinets with doors and open shelving. Notice how much natural daylight is available from the Solatube skylight.
Stainless Steel
Stainless steel cabinetry is an obvious consideration due to its superior durability and to the inherent cleaning in animal care settings. Consider just a stainless steel counter top on legs with no base cabinet for food prep areas. It is also easier to clean the floors under these prep counters. Stainless cabinets/tops are usually fabricated by a restaurant or kitchen equipment company. In fact, consider buying used stainless steel kitchen equipment, which can be very cost effective. One of my clients purchased used stainless steel free-standing storage cabinets for their cattery. The cabinets were movable, much less costly than custom built-in cabinetry, and met every need for a custom-built center island.
Hardware
The cabinetry hardware includes the pulls or knobs, slides for the drawers, hinges for the doors, and adjustable brackets for the adjustable shelves. Always use good quality hardware. Quality hardware ensures simple and efficient operations of opening doors and drawers and longer use in a high-wear environment like a boarding kennel. The architect has experience with hardware that has better tolerances, availability, and endurance. Discuss the hardware finishes with the architect or cabinet maker, and ask for recommendations. As an example, a brushed chrome door pull may complement the laminate and counter top better than polished brass. Consider self-closing doors and drawers. They are a little more expensive, but I think they are worth it if your budget allows.
Fabrication and Installation
It is my recommendation that the cabinetry goes through the construction submittal process. The contractor must submit the cabinet selection and drawings to the architect for your final approval. This includes drawers/cabinets, colors, hardware, etc.
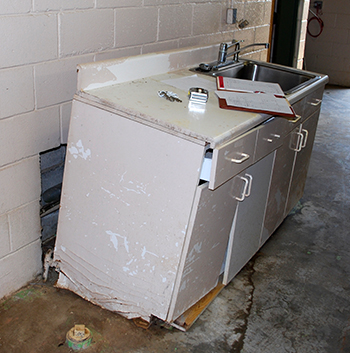
The bottom of this inexpensive base cabinet located in the dog kennel room of a boarding kennel has failed due to water intrusion.
The cabinet dimensions should also be field verified before manufacturing even though some contractors use the dimensions on the drawings. This is one of those checks and balances issues for me. I have seen too many times where the cabinets came in too short for the actual construction, and fillers have to be used to make up the gaps. This is just not good construction.
Field measuring and verification also goes for equipment installed with the cabinets such as dishwashers and refrigerators. If these are owner furnished and the dimensions are not coordinated, retrofitting can be an expensive proposition. This also applies to clearance for drawers and door swings. A cabinet door or drawer that won’t open because an appliance is in the way is a common observation. I actually have one of these non-functioning drawers in the kitchenette in my office building. My wife can’t blame me; I wasn’t the architect. But it does rob us of one more place to hide our stuff.
Richard S. Bacon, AIA, is owner and principal architect at Bacon Group, Inc., an architecture firm that specializes in the design of animal care facilities. With over 35 years’ experience, Rick is a registered architect, member of the American Institute of Architects, credentialed by the National Council of Architectural Registrations Boards, a LEED Accredited Professional in sustainable design, and a licensed General Contractor. He is a frequent workshop presenter on a variety of design topics for the boarding, veterinary, and animal humane care communities. He may be contacted by phone at 800-961-1967 or via email at [email protected].